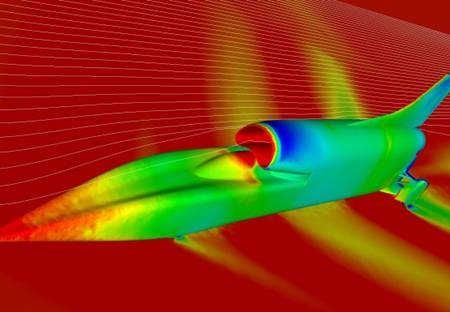
With just about a year to go until we are planning to run BLOODHOUND, a lot of things are coming together and it’s feeling more ‘real’ every month. After more than 7 years of work, our 3-engined Car, weighing 7.8 tonnes fully fuelled, is coming together as planned.

The upper chassis has now been stripped down and sent away to be anodised, which will improve its corrosion resistance. We won’t be driving BLOODHOUND in the rain, or parking it outside very much, but Hakskeen Pan’s surface is a very fine alkaline mud – it’s quite corrosive and it will get everywhere! When the anodised components return in September, it will be time to rivet and bond it together permanently: another major chassis component completed. With the upper chassis complete, we can then hang the EJ200 engine in the Car for the first time, which is going to look great. This sits over the top of the Nammo hybrid rocket, which is being test-fired in Norway as I write. If you haven’t seen our very first hybrid test firing, which proved the initial concept back in 2012, then have a look at this video – it’s impressive!
For the current Nammo tests, the concentrated hydrogen peroxide (known as ‘high test’ peroxide, or HTP) is being pressure-fed into the rocket with compressed gas. For further tests later this year, we will be using higher pressures (up to 76 Bar/1000 psi) from the BLOODHOUND rocket pump, driven by our 600 hp race car engine.
While we’re busy building this amazing 7.8 tonne Car, and testing all 3 engines, a recent question made me stop and think. The question was ‘why does the Car need 3 engines (jet, rocket and rocket pump) – does it have to be this big and complicated?’

A simple answer is that we’re trying to travel at jet fighter speeds (actually, 1000 mph at ground level is slightly faster than any jet fighter has ever been), so we’re bound to be a similar size.
The Eurofighter Typhoon is almost 3 metres longer than BLOODHOUND, and twice the mass, so the Car is really quite small by comparison.
It’s a bit too simplistic to compare the world’s best jet fighter directly with the world’s fastest car like that. The fact is that we could probably build BLOODHOUND smaller and lighter, but maximum speed is only one of the requirements. We want to build a safe car, and then make it go fast. So what does ‘safe’ look like and why does it require 3 engines?

For a Land Speed Record Car, ‘safe’ is a fairly simple concept: all you have to do is keep all the wheels on the ground, all the time. After more than 5 years of the most advanced computer modelling in LSR history, we’re confident that the Car will stay on the ground. However, just being confident is not enough.
We need to prove that the Car will stay on the ground, by doing step-by-step testing. This requires a power source that we can control. We’re also going to want to do around 40-50 test runs, gradually increasing the speed over the next 2 years, before we try for a 1000 mph Record.

With limited funds, that means we need a cheap-to-run, controllable and reliable engine. Bring on the EJ200, a life-expired development engine from the Eurofighter test programme, and now enjoying a second stint with BLOODHOUND. Supported by Rolls-Royce, the EJ200 will give us the cheap and reliable power we need for most of our test runs over the next 2 years.
The EJ200 by itself will get us to around 700 mph, not much faster. Even the Typhoon, which has 2 of them, will not reach 1000 mph at ground level, where the air is ‘thick’. We’re going to need a lot more power. This is where the Nammo hybrid rocket comes in. On top of the EJ200’s 9 tonnes of thrust, Nammo’s task is to provide us with another 12 tonnes of thrust for 20 seconds. The choice of a hybrid rocket is again made for safety reasons, not just performance.
The hybrid rocket consists of a solid fuel grain in the rocket tube, plus a liquid oxidiser which is forced in under pressure. The solid fuel is hydroxyl-terminated polybutadiene (or ‘HTPB’ among friends), which is just synthetic rubber. So far so good, as rubber is about the safest fuel you can have.

To make it burn at over 2500 deg C, we need to generate very hot oxygen, by forcing the hydrogen peroxide (HTP) through a silver catalyst pack. HTP is not explosive and it doesn’t burn (more safety points), but we need to be very careful with it, as it makes lots of other things burn really well!
The HTP is fed at 76 Bar (1000 psi) at over 40 litres/second, by a unique pump spinning at 10,000 rpm. Turning this pump takes a lot of power, which is what the 600 hp race car engine is for. Of course, we could just pressurise the HTP tank to 1000 psi, which would make the system much simpler and lighter – or would it? To keep the pressure up as the tank empties, we would need a set of high-pressure gas bottles, plus a system of large pressure-reducing valves. The tank would also need to be hugely strong, to support 76 Bar (which equals 760 tonnes of pressure per sq metre – that’s a very strong tank).

Based on our calculations, the mass of gas bottles, plus valves, plus super-strong tank, would easily exceed the mass of the race car engine, so there’s no benefit in a pressure system. But once again, the big decider is safety. If you have a leak in a system with a pump, you shut the pump down and it stops immediately. If you have a leak in a system pressurised to 76 Bar it will be spectacular, and not in a good way. Pump-fed may be more complicated, but it’s much safer.
Starting with the requirement to make the Car safe, then fast, we chose a jet engine for cheap, controllable and reliable testing, a hybrid rocket to deliver the big increase in thrust using (relatively) safe fuel components, and a race car pump motor to control the pressure. So to answer the question, do we really need 3 engines? Yes, we do, to get BLOODHOUND SSC to 1000 mph as safely as possible.
Of course, there is another question to ask. If we were starting again now, knowing everything that we’ve learned over the past 7 years, would we still choose the complex and heavy 3-engined design? I don’t know. In developing the shape for the world’s first 1000 mph Car, we’ve learned a huge amount, and developed a lot of technology.
Hybrid rockets have also come on a long way, with Nammo now testing a rocket system that may allow us to vary the power output, so perhaps we could do without a jet engine if we had to. But BLOODHOUND is not about ‘perhaps’, and part of the challenge of the Land Speed Record is that there is only one vehicle, so we have to live with the choices that we made at the start of the Programme. Our first prototype and is also our Record Car. It doesn’t need to be perfect, it just needs to be good enough.

Meanwhile, the ever-growing BLOODHOUND Education Programme can get the scientists and engineers of tomorrow working on BLOODHOUND Mark 2 – starting with the big question of how many engines ...
The penalty for our 3-engined safety-first approach is a more complicated Car, but with world-class partners like Nammo and Rolls-Royce, these problems can all be solved.

The BLOODHOUND team is also doing an amazing job, and at this point I have to mention systems engineer Joe Holdsworth, who has just got all of the Car’s electrical systems and hydraulics working for the first time, powered by the Typhoon’s ‘AMAD’ (aircraft-mounted accessories drive) gearbox. This has taken months of work and is a real achievement. Joe and the team have made something really complicated look simple. With people like this on our side, we’ll get there!