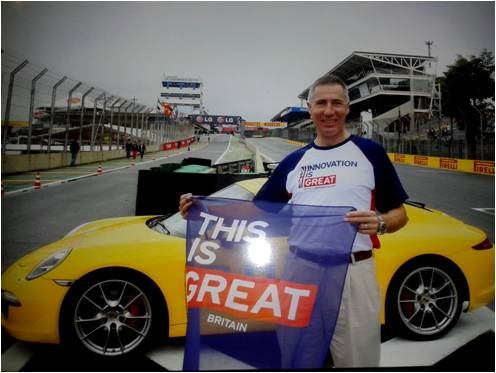
Global interest in Project BLOODHOUND continues to grow. I’ve spent a fair bit of the last month overseas, promoting the world’s first 1000 mph Car, together with BLOODHOUND’s science and technology education programme. Of course that involves promoting the world class engineering behind this British race car, too.
I spent five chaotic days in Brazil, in support of the ‘GREAT Britain’ Campaign. Presentations and press events covered BLOODHOUND SSC, the UK technology behind it, and our aim to inspire the next generation with the magic of science. I also visited a number of schools and colleges to talk about The Project and our Education Programme. Brazil is keen to reproduce this, as they need engineers just as much as we do. With some 5500 schools and colleges signed up in the UK, it’s already working well over here. If your school isn’t taking part already, then sign up to BLOODHOUND Education here. It’s free and it makes science lessons fun – what’s not to like?
The highlight in Brazil was the Formula 1 Grand Prix weekend, with the ‘GREAT Britain’ Campaign well-represented. First up was a symposium on ‘F1 in Road Safety’. How does that relate to BLOODHOUND? More easily than you’d think. At some level, all of the presenters, from F1 to DHL to BLOODHOUND, have the same basic aim: we’re all about ‘Speed and Safety’.
I was amazed at just how popular BLOODHOUND is in Brazil, not only with the schools and technical colleges, but also the Brazilian TV and press, the F1 circus and even the drivers. Emerson Fittipaldi, who was also speaking at the Road Safety event, wanted an autograph for his kids! BLOODHOUND really has become a global Engineering Adventure. At the track, I was lucky enough to get a lap in a Porsche 911, and sneaked in a quick bit of ‘ambush marketing’ for the GREAT Campaign.
As part of the Campaign, the British Consulate invited a number of visitors to see UK engineering expertise at work, which is exactly what F1 really is. Of the 11 teams racing in the series, no less than 8 of them are based in the UK, because, quite simply, we’ve got the world’s best racing engineers. Even a great German technology brand like Mercedes makes its F1 race cars, and its F1 engines, in the UK. Combine that with one of the world’s best aerospace industries and you finish up with the world’s best Land Speed Record vehicles as well. BLOODHOUND SSC is just the latest in a long line of world-beaters.
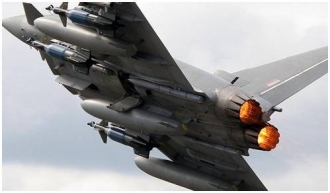
I recently had a chance to help promote the UK’s aerospace expertise, when I was invited to the Dubai Air Show, by Eurofighter and Eurojet. Dubai is an important air show for them, and they wanted something exciting as the focus of their Air Show Reception, so naturally they asked BLOODHOUND. We’re using perhaps the world’s best military jet engine, the Eurojet EJ200, so it gave me the perfect chance to thank them in public, in front of an international audience.
The choice of engine is not just about how much power it produces. Size and weight are also important, and we also need to think about the amount of fuel it will use (not much for the EJ200 – more of which later). The other big thing for me (given that I’m going to strap myself to it) is its safety record. BLOODHOUND SSC is aiming for over 1000 mph, which is faster than any jet fighter has ever been at ground level, so we’re taking the engine outside its design envelope. A big concern for us is ‘engine surge’, which is a breakdown in the airflow through the engine. This can cause the airflow through the engine to reverse, with the high-pressure gas in the centre of the engine being violently forced out through the engine intake. In simple terms, the engine sneezes.

The huge extra pressure of an engine surge can damage the engine intake. BLOODHOUND’s intake is being stressed to survive a surge, but multiple surges could do a lot of harm. If the intake fails, the pressure of the surge will probably explode the Car’s bodywork as well. That’s when it becomes a real problem, as we have no idea what would happen after that. The simple solution is to pick an engine that never surges, whatever you do to it – and that’s the EJ200. Back in 2011, while I was deployed with the RAF to support the air campaign over Libya, I saw the RAF’s Typhoons fly over 3000 combat hours, without a single engine problem. That’s simply astonishing. I’m very happy that I’ll be strapping myself to a jet engine with that kind of reputation.
Even when the jet is working normally, BLOODHOUND’s engine intake has to work hard. At 1000 mph, the pressure in the jet intake is around 1.7 Bar (25 psi). The pressure tries to force the 2 halves of the intake apart with a load of some 29 tonnes. It’s also feeding the engine with 75 kg of air each second (about 65 cubic metres/sec). If you want to picture 65 cubic metres, then compare it with the volume of the average UK house, which is about 200 cubic metres. BLOODHOUND’s jet engine would suck all the air out of the house in 3 seconds.
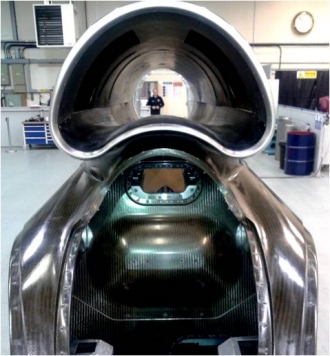
The intake components are manufactured with a small amount of extra carbon fibre material, so that they are slightly over-sized. This is the only way to guarantee a perfect fit: make them slightly too big and then trim them. The challenge with the intake is trimming the ‘B’ surface (the inside of the intake ‘tube’ is moulded, while the ‘B’ surface is the rough surface on the outside of the tube, hidden inside the bodywork). This ‘B’ surface has to plug into the moulded inner section of the monocoque, above and behind the cockpit. The only way to check the fit is to climb and do it from the inside. We haven’t seen much of our expert fabricator, Tufty, recently as he’s spent a lot of hours in this small dark space, trimming the world’s fastest jet engine intake.
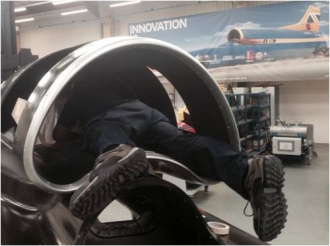
URT continues to produce top-class carbon bits for the Car, with the mould for the jet engine’s fuel tank now completed. It’s an odd shape, designed to make full use of the available space underneath the front of the engine. Despite BLOODHOUND being 13 metres long, we are using just about every millimetre inside it. The main jet fuel tank holds around 400 litres, which doesn’t look much. However, it’s enough for a 5-minute engine warm up, a full-power run to supersonic speeds, and then 2-3 minutes cooling down before shut-off.
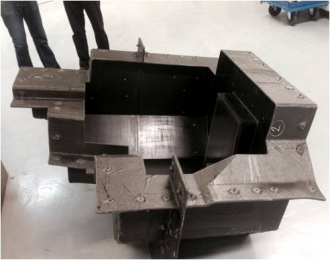
We’ll also have 2 auxiliary tanks further back in the Car, just in case, as the performance figures could be a few percent out. After all, no-one has ever done this before and the engine has never been this fast at ground level.
The front suspension sub-assembly is well under way at Boeing AMRC in Sheffield. I love the fact that they are using one of the fastest aluminium cutting machines on the planet (spindle speeds of 30,000 rpm) to make major parts for the fastest car in the world.
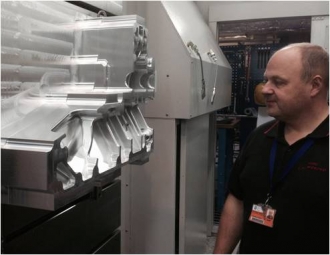
We’ve also had more components arriving for the rear suspension. BLOODHOUND SSC needs over 3500 bespoke parts and a steady supply of these from the 250+ companies supporting the Project means we can crack on with the assembly. As Chief Mechanic Chris Dee recently said of our summer 2015 target date to run in South Africa, ‘Keep the parts coming and we’ll beat that!’. Go to it guys, the world’s waiting to see the finished result.
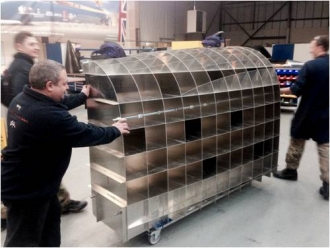
All of the Car’s 2D titanium skins have now been completed, for the sides of the rear upper chassis. ‘2D’ means they are only curved in one direction, like the surface of a cylinder. The much more difficult bit is right at the back on the Car, where the curves are ‘3D’, like the surface of a large ball. These panels are still made by hand and, for the 3D shapes, are hand-formed to fit a ‘buck’.
The buck is made from a series of aluminium sheets, which can be assembled either right or left-handed, so we can use the same buck for both sides. This will – hopefully – make it easier to produce symmetrical panels for both sides. The Hexagon metrology laser will reveal all when we assemble the panels over the next few of months.
Meanwhile, this is the last time we will ever see the Car’s ‘skeleton’ fully assembled. The next time we put it all back together, it will have the skin panels glued and riveted in position, and we’ll be getting ready to run it for the first time. Can’t wait.
Last Time With No Clothes On
The rainy season in the Northern Cape of South Africa has started now, with plenty of rainfall in recent days. This is good news, as every wet season helps to smooth the repair work and track preparations on Hakskeen Pan, in advance of our first runs in 2015. The Northern Cape team probably has around 2 months of tidying up work left to do next year, moving the piles of stones already cleared from our track and filling the last of the holes left behind. The Fastest Track on Earth is nearly ready for us.
2013 has been a really good year for BLOODHOUND. The Car is rapidly coming together, and each time I see it there are new parts fitted and more work completed. We’ve also just signed a couple of major new deals, so 2014 is going to be just as exciting, as we announce some new partnerships and reveal some more technical developments. I hope you are all looking for to the New Year as much as we are. In the meantime, have a Supersonic Christmas!
Andy Green