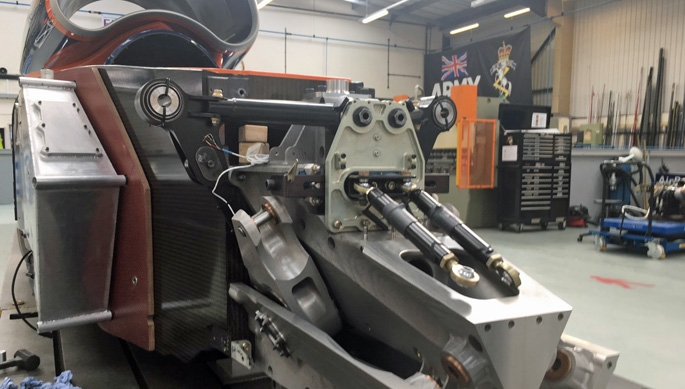
Putting it all together
Piece by piece, BLOODHOUND SSC is coming together. While the process is slow, it’s exciting to see more bits of the Car working for the first time, ready to start testing the Car later on this year.
Joe and his systems team have done a terrific job of getting all the jet engine’s systems to work. If might sound simple to spin up a gearbox and get the generator to produce electrical power (after all, it happens every time you turn the key to start your car). However, aircraft systems are very fussy about the voltage and frequency of their power supplies – apart from anything else, the Typhoon’s twin engines have to match their electrical outputs exactly, so that they can both feed power the aircraft.
The Typhoon, like most aircraft, has both direct current (DC) and alternating current (AC) power supplies. The standard specifications for aircraft power supplies were chosen long ago, for very mundane reasons. For the DC system, ‘standard’ batteries (like the one in your road car) produce 12V. To give a bit more ‘oomph’ for aircraft systems, they double up the number of cells to make a 24V battery and, as the generator needs to produce slightly more than 24V to keep the batteries charged up, it’s a 28V system.
The AC generator produces 3-phase power at 115V for each phase (115V being a common domestic US voltage – told you the specifications were mundane). 'Three phase' is a type of electrical power delivery commonly used in industry and aerospace. Alternating current, as the name suggests, switches between being positive and negative at high frequency. In the UK, the domestic electricity supply cycles 50 times per second (50 Hertz, or Hz for short) while US systems run at 60 Hz, while aircraft systems keep their size and weight down by running at a much higher frequency of 400 Hz.
During each cycle there are 2 brief moments when the power output is at zero. In order to avoid these ‘dead spots’ in the power delivery, heavy industrial electric motors (and some aerospace applications) use 3 ‘live’ wires to supply 3 phases of AC power, which are sequenced so there are no dead spots.
Unlike aircraft systems that need multiple redundancy in case something stops working, BLOODHOUND can get away with having just one generator. The Car’s EJ200 jet engine drives an AC generator producing 3-phase 115V AC at 400 Hz (as described above). This AC power drives the Car’s high-pressure fuel pump (rescued from a scrap Tornado), supplying the jet fuel needed for full reheat. The AC generator also feeds a transformer-rectifier unit (from the same scrap Tornado) which drops the 115V AC down to 28V (the ‘transformer’ bit) and then converts the AC to DC (the ‘rectifier’ bit). This provides BLOODHOUND’s 28V DC, which powers nearly everything else in the Car. Aircraft batteries (24V) power all the systems when the jet is not running and provide some redundancy in case the generator fails.
Generator in place, waiting for its jet engine
Now for the tricky bit. Our jet engine’s AC system has some very clever electronics. The generator supplies electrical power under the control of a series of boxes with not-very-interesting names like ‘generator control unit’ and ‘current transformer assembly’. These boxes expect to ‘talk’ digitally to the Typhoon in order to monitor the aircraft’s power requirements…. but our jet engine is in a Land Speed Record Car and there is no Typhoon to talk to, so BLOODHOUND’s software has to ‘trick’ the generator system into seeing what it needs to see.
This is the really impressive bit of what the BLOODHOUND team has achieved. It’s not just spinning up a generator to get power, it’s creating a virtual aircraft (in other words, it’s a big fat software fib) in order to keep the generator system happy. I can’t claim to understand how the team has done it, but it works, and BLOODHOUND can now generate its own electrical power.
The ‘optimised’ Goat’s Head
Another major piece of work last month was the build-up of the front suspension assembly, around what is known as the ‘goat’s head’. This is an aluminium structure that supports the front wheels, suspension and steering (so, speaking as the driver, it’s quite important!). The front suspension may have to support loads of up to 300 kN (30 tonnes of force), to cope with aerodynamic loads, bump loads, and so on. The goat’s head structure has to be both light and hugely strong, and was designed using a fascinating process.
Like most parts of the Car, the goat’s head was designed using CAD (computer-aided design) software. The interesting bit is how the team worked out the shape of the structure, using a technique called ‘topological optimisation’. This is a software technique that starts with a solid block of virtual ‘metal’ in the computer.
The computer simulates the solid block attached to the chassis (in this case, the front of BLOODHOUND’s carbon fibre monocoque), with simulated suspension attached to the outside of the block. The ‘optimisation’ (some very clever software) then removes all the bits of ‘metal’ that are not carrying any load, leaving only the bits that are needed. This process is shown in our latest ‘Anatomy of the Car’ video, which also explains where the name ‘goat’s head’ came from.
Assembling the finished article
Once the design was complete in CAD, the electronic shape was machined from solid aluminium billet. This is a good way of producing one-off components, albeit with a lot of material left over to be recycled.
The various parts of the goat’s head were made on a 5-axis machine at AMRC Sheffield, taking a total of 97 days of machining, which gives an indication of the complexity and precision required. To give you an idea of the weight savings made through the design process, the solid billets at the start weighed a total of some 924 kg. By the end of the process, the bits that make up the goat’s head weigh just 68 kg, with 856 kg of trimmings to be recycled. Less than 8% of the original mass remains, now assembled and ready to support loads of up to 30 tonnes. This is one of those facts that makes engineering seem like magic sometimes….
Optional ballast
The first test runs of the Car this year, at the Aerohub in Newquay, will be jet-only, as our rocket system is still in development. Despite this, the HTP tank (for the rocket oxidiser) is being finished off and fitted into the Car, even though we’re not going to use it, which initially surprised me. I assumed that we’d be running the Car as light as possible, but it turns out there’s a simple explanation.
Fitting the HTP tank gives us the option (if we need it) to add water ballast, moving the centre of gravity forwards and making the Car more stable. While UK runway testing is ‘slow speed’ in BLOODHOUND terms, we’re still aiming for 200+ mph, which is not to be sniffed at, so we want the Car’s handling to be at its best from day one.
The rubber tyres should give us good lateral grip on the runway surface and, having spent a (very exciting!) career driving Royal Air Force jets down runways at up to 200 mph, I doubt that we’ll need the extra ballast. However, right now that’s just a guess. The secret to success in a project like this is to have answers for all the problems we know about, plus some just-in-case answers for the problems we might have. We can’t be certain until we try it – that’s why we call it an ‘Engineering Adventure’.