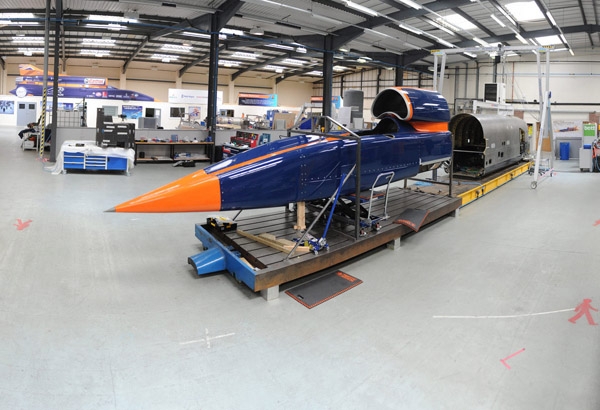
Watching the final assembly of the world’s first 1000 mph Car, some things are more obvious than others.
The obvious bit is the mechanical assembly of BLOODHOUND SSC, as the chassis, body work, suspension, etc., is delivered to the BLOODHOUND Technical Centre and fitted for the first time. Rather less obvious is the stuff that makes the Car ‘work’ – in other words, all the systems, including electrical power, hydraulic power, electronics, computers, sensors and so on. A quick look around the Technical Centre shows that the systems team is now bigger than the mechanical build team. This is increasingly where the action is.
Being a systems engineer can be a bit of a thankless task, as you have to wait until the mechanical team have built quite a lot of the Car, before you can go to work fitting wiring, sensors, etc. Worse still, starting last means you’re probably going to finish last, which in turn means that everyone will be waiting for you, and asking if you’re finished yet…. That’s probably a glimpse of the near future for our systems team. Apologies in advance, guys: we’ll try to be (a bit) patient!
Titanium is strange stuff
Before we can complete the systems installation, we’ve got to finish the mechanical build of the Car. The RAF technicians from 71 Squadron seem to be all over the Car at the moment, as they come near to the end of their work packages for BLOODHOUND. At the front end of the Car, the cockpit is up in the air while the bottom sections are completed. The cockpit sits directly behind the front wheels, which will throw up a fearsome supersonic dust storm at high speed. To survive this extreme environment, the bottom of the Car is being panelled in titanium.
Titanium has some strange properties. It’s very strong (which is why we’re using it) but it’s also difficult to work. The metal sheet has a ‘memory’, which caused us a problem in making the curved bottom edges of the Car. After being put through the panel roller to curve it, the sheet simply straightened itself out again. Not quite what we were after.
One option is to heat-treat the metal, to ‘set’ the curve, but the very high temperatures required would soften the panel too much. After some more thinking, one of the team worked out that a shallow ‘crease’ should hold its shape in the metal, and enough creases should bend the sheet through 90 degrees. A day’s work and 22 precisely-made creases later, we’ve got a quarter-round titanium panel and the assembly continues.
Rear deltas and the RAF
At the back end of the Car, the RAF team is now finishing off the preparation of the rear deltas. These fairings cover the rear lower suspension arms, looking like a cut-off triangle (or ‘delta’ shape) when seen from above. Once these are complete, we can start to assemble the rear suspension for the first time.
Like you find in a chicken – sort of
In preparation for rear suspension assembly, we’ve just taken delivery of the last major parts, the rear ‘wishbone’ elements which connect the wheel ‘uprights’ to the chassis. In simple terms, the upright contains the wheel bearing and hub, and is connected to the Car by 2 horizontal V-shaped pairs of struts call ‘wishbones’ (like the bone you find in a chicken). Can’t wait to see the Car on its wheels for the first time.
The Fin is still being assembled, but hopefully not for much longer. I was sitting through a meeting recently in the Technical Centre, when I heard the distinctive 'ker-bang.. ker-bang.. ker-bang...' noise as 71 Squadron started to put pop rivets into it.
The pop rivet is a fascinatingly simple device, which can be used when there is only access to one side of the panel being secured (we can’t get access to the inside of the Fin once the panels are in place), hence they are also known as ‘blind’ rivets. A central metal stick, called a mandrel, is mechanically pulled out of the rivet, with a lump on the end of the mandrel forcing the rivet to expand into the hole, before the mandrel breaks off and leaves the rivet in place. This operation is done quite rapidly with a pneumatic gun, hence the 2-part ‘ker-bang’ noise as the mandrel is pulled through the rivet, then breaks off with a bang to complete the job. If that sounded complicated, have a look at our latest Cisco BHTV video, as it really is a simple device.
Almost Fin(ished)
The rivetting means that after months of work, the world’s hardest-working tailfin is being put together permanently. Another bit of the Car assembly being finished. Now we can start thinking about painting it and then ‘wrapping’ it with its Union Flag design, including some 30,000+ names. Want to put your name on the world’s fastest Fin? Sign up here and you too can travel supersonic next year.
Once the mechanical build of the Car is complete, we’ve still got to complete and test all of the systems. The systems team is getting as much of this done as they can, building wiring looms and bench-testing components, so that they are ready to drop into the chassis once the build team can is nearly done.
Generating some technical challenges
Last week I watched the jet engine’s gearbox being spun up to 60% of maximum speed (that’s lots of thousands of revs/min) to check the generator output. Good news – it worked. Bad news – as soon as we tried to run an electrical load (a fuel pump), it stopped working. We’re now busy trying to convince the system’s software that it really is in a Typhoon, and that everything is working properly, so that it will give us power under load. If we want to use the world’s best military jet engine, the Typhoon’s EJ200, then we’ve got to work for it. It’ll be worth the effort.
While the cockpit is up in the air, having the Car’s floor fitted, the cockpit panels sit in the corner of the Tech Centre, gradually being wired up. At Version 20 of the cockpit design, I’m hoping we’re just about at the final layout, as we’ve now got to build it. I started designing Version 1 in June 2008 (I’ve just checked), so we’ve been working on this for a while now! It’s not that I keep changing my mind (well, not only that). As the power and control systems develop, we sometimes need to change how I monitor and control them.
For example, we’ve recently finalised the design of the Car’s fire system and taken delivery of the Car’s ‘Lifeline’ fire extinguishers. We’ve got 7 extinguishers on board: 3 using water and 4 using a fire-inerting gas called FE36 (which is 1,1,1,3,3,3 hexafluoropropane, in case you were wondering). The FE36 is for the nose section, the cockpit, the rocket pump bay and the jet engine bay, and the water (in the unlikely event of an HTP rocket oxidiser leak) is for the HTP tank, pump and rocket bays. We’ve chosen to operate each of the extinguishers manually, so the cockpit needs 7 buttons in the correct layout, matching the bay positions in the Car – this change is Version 20 of the cockpit controls.
Version 20 – nearly there
Finally, despite my temptation to ignore it, I suppose I should mention my small ‘moment’ (OK, crash) in the Jaguar Rapid Response Vehicle at the Goodwood Festival of Speed. I’ve already apologised to Jaguar (who were very nice about it) and the BLOODHOUND team, so for completeness, my apologies to anyone looking forward to seeing the car running up the hill, I’m sorry we didn’t make it as far as planned.
One of 300 successful rocket cars
It’s disappointing that we ran over 300 rocket cars during the Goodwood weekend, and every one of them managed to get to the other end of the track, while I failed in my one attempt to get to the top of the hill.
Driver aids
To make matters worse, and just in case the tens of thousands of spectators hadn’t all noticed, I had Ray Massey from the Daily Mail in the car with me, so we’re now (in)famous with the whole of Goodwood and the whole of the Daily Mail readership. They say all publicity is good publicity, but in this particular case, I’m not feeling it, even after the team came out with some helpful pedal labels for next time. I’m glad we don’t have to worry about corners in Land Speed Record racing.
To finish on a high note, BLOODHOUND supported this year’s Science, Technology, Engineering and Maths (STEM) day at RAF Scampton, which was laid on by the Red Arrows. Despite all the cool ‘STEM’ technology on display (a Land Speed Record car, a Formula 1 car, various ‘slower’ vehicles, robots, explosions, rockets, etc.), the biggest draw of the day was, of course, the Red Arrows.
Great British engineering
Despite the mediocre English summer weather (rain), they put on their amazing flying display during the lunch break. Great British expertise (both flying and engineering) at its very best. It’s this level of expertise that’s going to help us to build and run a Car capable of 1000 mph. It’s going to be quite something to watch.