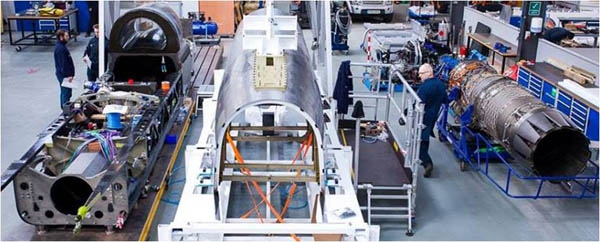
As we get closer to completing the most extraordinary straight line racing car in history, it's easy to forget the most important part of building the world's first 1000 mph Car. Getting to 1000 mph safely is not just about technology, it's about engineering expertise, an area where Great Britain is still among the best in the world. This is why I'm not worried about driving BLOODHOUND SSC later this year. Quite simply, I trust the BLOODHOUND engineers, because they are world-class.

This world-class expertise was recognised this month at the annual 'SEMTA' Engineering Awards. BLOODHOUND's Chief Engineer Mark Chapman was elected to the SEMTA Hall of Fame, alongside some of the most famous names in engineering, including Brunel, Stevenson and Whittle. This is public recognition of true world-class quality – well done Mark!
Project BLOODHOUND is all about promoting engineering, and inspiring the next generation with the excitement of science and technology. The recent front-page feature and video by the Financial Times (among many others) highlights the 'BLOODHOUND effect' of engineering promotion. But are we really reaching young people and creating an interest in engineering? The answer is a resounding 'yes'. To quote just one example, Castle Precision Engineering (which is making BLOODHOUND's wheels) is already seeing a huge difference. Castle's Managing Director, Jan Tiefenbrun, quotes the level of apprenticeship applications: when Castle started working with BLOODHOUND 5 years ago, 'for 8 apprenticeship positions we had 50 applications'.
For a precision engineering firm like Castle, that's not really enough to guarantee the quality of apprentices they need. Now, thanks to BLOODHOUND, 'We had 6 places for apprentices in 2014 and 600 applications'. That's the 'BLOODHOUND effect' at work.

Castle Precision has previously made our 'slow speed' (slow for BLOODHOUND means 250+ mph) runway test wheels. This month Castle has been machining the high-speed desert wheels for our 800 mph runs later this year in South Africa.
The BBC's Jon Amos was there to press the button and start the process: you can read his article on the wheels here. I was lucky enough to see these wheels starting life over a year ago, forged by Otto Fuchs from solid blocks of aluminium. Each quarter-tonne block was heated to 380 deg C and then squeezed like putty in a huge 3600 tonne hydraulic press. Repeated forging (squeezing) aligns the 'grain' of the metal, making the wheels very strong. Watch the video here – it's an amazing process.

These high speed wheels need to be incredibly strong. At 1000 mph, they will spin at over 10,000 revs per min, with loads of 50,000G at the wheel rim. We know they are strong enough to cope with these incredible loads, thanks to the high-speed testing of our first test wheel.
In the fastest spin test ever conducted on their engine test rig, Rolls-Royce proved that the wheel would survive the 50,000G loads, and that our engineering predictions were spot on. You can watch the world's fastest wheel spin test video here to see why we've got such confidence in the end result.
Despite this, our engineering team has gone a stage further and looked at possible failure modes for the wheel. It is just possible (although very unlikely) that a wheel could pick up damage on the desert surface, perhaps by hitting a stone buried just under the surface. If this happened, it's also possible (but even more unlikely) that a chunk of wheel rim could break off at maximum speed. What effect would this have on the Car? Could this chunk of metal, travelling at around 1000 mph, punch a hole in the cockpit, for instance? To counter this risk, the cockpit sides have ballistic armoured panels and we've just tested them.

Morgan Advanced Materials tested the armour in their firing range and the news is very good. The largest practical chunk that might fly off the wheel will easily be stopped by the armour. In fact, it's even better than that. The estimated maximum energy from a wheel fragment is around 22.5 MJ (22,000,000 joules) of energy – enough to boil 60 kettles instantly and equal to the energy of a cricket ball travelling at 1175 mph. The test at Morgan Advanced Materials went further, firing a 'sabot' (or bullet) at 2300 mph, giving an impact of 29 MJ (equal to a cricket ball at 1334 mph). As you can see from the test video of the firing, the sabot did not penetrate the armour, showing that the cockpit is safe from pretty much anything thrown up by (or thrown off) the front wheels.

One of the challenges of driving on solid metal wheels is the low grip levels, particularly on the dry mud surface of our track in the Northern Cape of South Africa. For rubber tyres on a tarmac road, the 'coefficient of friction' is about 1.0: in other words, the amount of sideways grip is the same as the weight of the car. For our dry lakebed track in South Africa, we're expecting a coefficient of friction of about 0.2 – about the same as driving on ice and snow. As a result, I was out in Switzerland last month to do a little bit of 'top up' training on car handling skills, in the new Jaguar F-Type All Wheel Drive. It's slightly counter-intuitive to go to a winter resort to practice high speed desert driving, but it was worth it, as I learned a huge amount about low-friction driving, steering and car balance. It was also great fun....
The build of the rest of the Car continues apace. This month we've installed the EJ200 jet engine in the completed upper chassis for the first time. This allows us to check all the clearances and mounting points. Everything worked as advertised, which represents another big milestone for the Project.

The other main power source for the Car is of course the Nammo rocket motor. The previous rocket firing was impressive enough. In a few weeks' time, we'll be firing it at even higher pressures, using BLOODHOUND SSC's pump system powered by the Jaguar V8 engine. We tested the pump last month, which showed that this 550 hp pump system was more than up to the task of pumping a tonne of HTP (rocket oxidiser) through the rocket in 20 seconds. After the test, we stripped the rocket pump as a matter of course. It was slightly disappointing to find that the rear bearing had not fared well – we'd pretty much destroyed it.

However, for fast-paced development engineering like BLOODHOUND, this kind of problem is normal business. We're fairly sure that the bearing problem was caused by a quirk of the test rig, which allowed loads to be transmitted along the pump shaft. To make sure, we're going to test it again shortly with a modified test rig. Then we're off to Nammo for the high-powered rocket firings, simulating the profiles that we'll be using later this year in the desert. An exciting time for the rocket programme – results to follow shortly!

The bodywork build continues, with the front carbon fibre panels being fitted and gradually drilled off. This is not as simple as it sounds. Carbon fibre panels are laid up in a mould, using multiple layers of woven carbon fibre impregnated with resin. The mould is then put into an autoclave (large oven) and cooked for several hours, to set the resin.

When the parts come out of the mould, they tend to 'spring' a little bit, taking on a slightly different shape. This is perfectly normal (if slightly inconvenient) for carbon fibre body panels. Each panel needs to be hand-fitted to the Car's chassis, to make sure every piece fits perfectly. If 1000 mph of airflow gets under a panel, the air pressure will peel it back with a force of up to 12 tonnes per square metre. That will quickly make a huge mess of the bodywork, so this vital process requires absolute precision in every detail.
It's great to see it coming together week by week. I can't help feeling excited as we watch it happen. In just a few months we'll be starting our test runs at Newquay Aerohub (want to come and watch? – join the 1K Club now). I don't know about anyone else, but I can't wait.