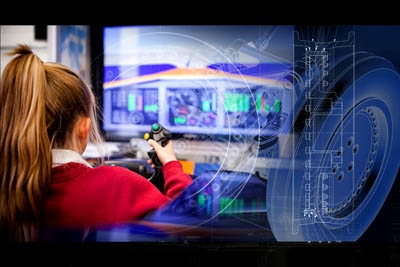
Imagine going along a road at 1,000mph – that’s about 15 times faster than you can go on a motorway. At that speed, you can’t take any chances.
The thing is, we don’t actually know what a car driving at 1,000mph would do. It’s never been done. Not for real. But it has been done ‘virtually’.
Just like in a computer game – where you can make things run, jump and spin around in a make-believe world on your TV screen – engineers can use 3D Computer Aided Design (3D CAD) to create imaginary objects and play with them in their own virtual world.
So before building and driving the world’s first 1,000mph car for real, the Bloodhound engineers have drawn it in CAD...and got it ready to take on a virtual test drive.

BloodhoundSSC Engineer
How does it all work? Let’s get Jenna Gaff, one of Bloodhound’s design engineers, to explain…
“Just like in a computer game, we need our imaginary world to ‘play’ in - so we use an axis system to create a virtual floor and to define the space above that floor as, well, a virtual workshop.
“Each design engineer has a CAD station and access to all the parts of the car and although lots of different people draw parts of the car, we all work in the same virtual workshop – so all the parts are positioned relative to each other.
“One of the neatest parts to draw is the body of the wheels – so let’s use that to explain how we do it.
“Basically, we draw a circle on the floor and give it a thickness - which in tech speak is called ‘extruding’ it or we draw a side profile of the wheel and revolve it. Both of these techniques will creates the same 3D shape – just like one of the wheels we’ll have on the Bloodhound car.
“Of course in real life, we need to fix the wheels to the car, so we need to put some detailed holes around the centre of the wheel – so we have to do the same on our CAD system, putting the mechanism and fixing process together on the virtual car to check it works and the wheels don’t fall of!
“We draw a number of small circles on the wheel surface and extrude them, then tell the computer to cut or subtract the small discs out from the big disc. That gives us a wheel with holes in the right places.
“And that’s it pretty much done - except the wheel we’ve just designed is currently lying on the floor and we need it to be attached to the car.
“And because it was designed in the ‘virtual workshop’, we know its location and the location of all the other parts so we simply pick it up and fix it to the right place – just like a car mechanic does with a real wheel.”
Thousands of individual 3D drawings were done and fitted together to create the final virtual car – then it was time to take it for a spin...
NEXT TIME: Taking Bloodhound for a ‘virtual’ test drive...