
Opening Bloodhound SSC’s Technical Centre
This summer Minister for Universities and Science, David Willetts MP, formally opened the new Bloodhound Technical Centre in Avonmouth, Bristol. It was a fantastic event with the Minister talking about the importance of UK skills and the increasing demand for Scientists, Engineers and Mathematicians.
Picture above: REME Corporal Lisah Brooking keeping a keen eye on Minister David Willetts MP. Image by Stephan Marjoram
And it’s this challenge that Bloodhound SSC intends to tackle – to inspire kids into STEM subjects by building a car capable of 1000 mph and allowing the student population to be able to engage and follow the project.
Bloodhound SSC’s new technical centre has been occupied for a few months while the team have been commissioning the site and getting all the workshop machines ready to go. The new centre looks impressive and provides the design team as well build engineers/fabricators with a great facility in which we will build the car. A special mention must go to SSgt Neil Gallagher who received a commendation from Director Richard Noble for his part in managing the move to the new Avonmouth site.
SSgt Gallagher got permission to extend his attachment by 2 months to see the move through to completion. He has since handed over to his successor SSgt Ben Richards who continues the role of Workshop Manager supporting Chris Dee (Build Manager) to ensure the machines are fit and are available at all times.
Picture left: SSgt Neil Gallagher with his commendation. Image by Stefan Marjoram
Introducing the new REME team
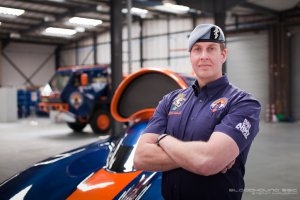
The composition of the second team of REME tradesmen has developed to reflect the changes and demands of the build as it continues. As we move into the assembly of the rear upper chassis, SSgt Ben Richards’ experience repairing aircraft on Operations comes to the fore. He has been helping to build the chassis rails that connect the carbon fibre monocoque to the rear lower chassis.
SSgt Ben Richards is one of two Artificers on the Army team. Artificers are the REME’s technical fast track managers and are amongst the most respected soldiers in the British Army.
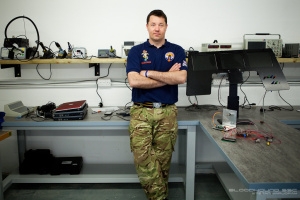
Alongside Ben, is SSgt Henry ‘H’ Breed who is an Electronics Artificer and works with Joe Holdsworth on the Bloodhound’s electronic control systems. He has continued AQMS Mark Edwin’s work prototyping EJ200′s control system as well as developing the electronics of a number control systems.
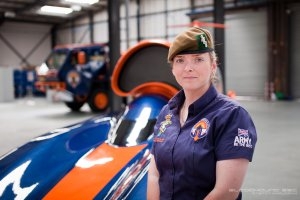
On the mechanical side of the project, Corporal Lisah Brooking has been working with Lee Giles on the rocket development system. She has done a fantastic job and has developed her technical knowledge testing the F1 engine’s custom gearbox at X-trac near Reading.
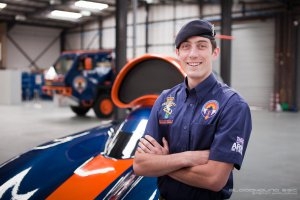
The last member of the team – and certainly not least, is Craftsman Andy Pike who is an Armourer and the youngest engineer on the whole project. Cfn Pike is normally found working in patrol bases repairing weapon systems with the Infantry. He has used his technical knowledge and manufacture skills to support some of the more senior fabricators assembling the car.
Project update…the build story so far
So what is happening with the vehicle build at the moment? We have been lucky that we could continue building the car whilst the building has been commissioned.
All of the workshop machines supplied under Bloodhound contract with the Army have been delivered (thanks SEAE and SEME) and the machine shop is now ready to start production of smaller components. The machine shop, with lathes, mills, folding and cutting machines, to mention a few, is an important addition to the Technical Centre. It will save time and provide agility when essential components are needed that can’t be sent to suppliers.
Positioned in the centre of the workshop, not far from the machine shop, is a huge surface table that the Bloodhound SSC car will be built on. So why do we need to build it on a metal surface 30 cm off the ground?
Surface table. Image Stefan Marjoram
We need an incredibly flat surface to build on to ensure that we can accurately measure the car as it is assembled – you wouldn’t want us to put it together wonky! Dan Johns, who has spent much of his career working with Airbus as a Manufacturing Engineer is using a laser scanning system to ensure that the car’s components are placed as accurately as possible in the X, Y and Z axis. David Willetts MP had the honour of tightening up the bolts that connect the lower chassis and monocoque together – all under the watchful eye of Cpl Lisah Brooking!
The most recent work has been the arrival of the chassis rails which have come back from the autoclave and are now fitted to the car. The fabrication team have done a great job, delivering ahead of time to assemble, Kephos (black anti corrosion paint), re-assemble/glue and cure – and with an accuracy of 0.4 mm variation over 6 metres.
So what’s coming next?
The lattice structure on the side of the car (where the red dot is) has been dry assembled to ensure that all of the resources required to complete the work package are ready to go. The combination of the chassis rails (green dot at either end) and the lattice will provide increased stiffness to the body of the car – in a similar way to that of a bridge.
Infantry bridge. Crown copyright
Chassis rails and lattice. Image Jules Tipler
Now that Dan Johns has laser scanned and measured the mating surfaces, we have the assurance that we will be building on an accurate and level plane which means that the jig can be made available to start to receive the initial sections of the upper chassis which has been designed similar to the construction of an aircraft. Within this structure, the EJ200 developmental engine will be suspended beneath the structure, with the fin supported on top!
The upper chassis is going to be a big job with over 11,000 holes to drill, prepare and rivet – I will keep you updated when the job starts and how it progresses.
Next blog I will be writing about the REME team and our time at Goodwood Festival of Speed talking to kids about engineering and science and Bloodhound SSC!