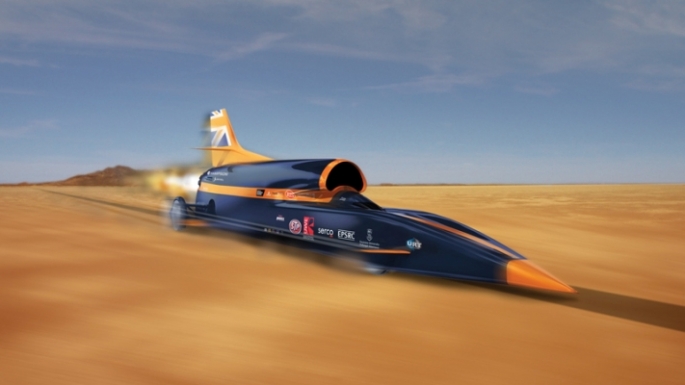
Some breaking news this month. We’ve been working on timings for the final build of Bloodhound SSC for a couple of months now, to see if it is practical to get out there by the end of this year. With some 200 technical partners, product sponsors and suppliers to include in the planning, it’s a wide-ranging conversation! We have also had to take into account the weather in the Northern Cape in South Africa, where we are going to run. The rainy season stretches from about November through to April, so the weather could stop us running during that period.
So here’s the new plan that we’re now going to deliver – we will be test-running the EJ200 jet engine in the Car in October of this year (our fifth Birthday: how time flies when you’re building a 1000 mph Car), followed by runway testing at the start of 2014 and then off to South Africa around Easter next year.
This is a slightly disappointing delay, as we won’t make it to the desert this year, but looking at the weather cycle and the build programme, it’s the right decision.
Great news on the engine tests and runway runs. We have now confirmed that we will be using the Aerohub @ Newquay Cornwall Airport for all of Bloodhound’s UK test programme
Rocket Testing at the Aerohub
The Aerohub was a fantastic venue for our rocket test last October (if you haven’t seen it already, you’ve got to watch the video!). Newquay is going to be a great location for our static engine tests in october and particularly for the runway runs. I know the airfield well, having flown jet fighters from there when it was an RAF base. The runway is very high quality and absolutely huge (9000 feet/2.7 km long), which is more than enough distance to get Bloodhound SSC up to 200+ mph and stopped again. A big thank you to Cornwall County Council and Newquay airport for their support – we can’t wait to get there and start work.
The first event at Newquay will be the next batch of rocket testing, in one of the old cold-war military aircraft shelters. For the first desert test runs, we will be using the monopropellant rocket in Bloodhound, which will give us the capability to get the Car up to around 800 mph. This will give us several things, including more data on the supersonic aerodynamics, a good test of the chassis and suspension – and of course a new World Land Speed Record. For our second test session (late 2014 or early 2015) we will fit the high-powered hybrid rocket (see the video above) and return to South Africa for the ultimate challenge – 1000 mph.
Both rocket configurations will use the same basic system which includes the catalyst pack, the high-speed pump and, of course, the world’s best pump motor, the Cosworth Formula 1 engine. We’ll shortly start testing this system again, in monopropellant mode, at the Aerohub in Newquay. In preparation, we’re now testing a key part of this system, the XTrac gearbox that transmits the 18,000 rpm drive of the Cosworth engine to the 11,000 rpm pump.
Assembling the World’s Fastest Gearbox for testing
While the rocket testing is about to start up again, the chassis build is pressing ahead. All of the final machining on the carbon fibre monocoque (which includes the cockpit) has now been completed by URT Composites. Bloodhound SSC’s chassis is made of from hundreds of components, made by dozens of different companies, and obviously we need to make sure that they are all exactly the right size and shape, so that they fit together perfectly – we don’t want anything falling off at 1000 mph..... The technique of component measuring is known as metrology, and we’re lucky to have a company called Hexagon doing it all for us.
Metrology by Hexagon
The manufacturing accuracy of some of the components is just astonishing. For example, the carbon fibre monocoque (my 1000 mph office) has been machined to within 6 microns of the specified size. To put that in perspective, a micron is one millionth of a metre. The average human hair is 100 microns thick – so the monocoque has been machined to less than one tenth of the thickness of a human hair. Like I said, accurate.
The 1000 mph office – accurate to 6 microns
The lower chassis is now ready for final assembly, which involves both bonding (engineering speak for gluing) and riveting. This lower section requires some 3000 rivets, which means 3000 holes precision-drilled through the body panels (which has kept the workshop team busy for the last few weeks). The bonding process requires the glue to be ‘cooked’ to make it set – 80 degrees C for 5 hours, in an autoclave (a very big oven) at the National Composites Centre in Bristol.
Getting ready for ‘painting’ and ‘gluing’
Before it’s all glued together, the various bits will be coated in one way or another. This is an important protection process for the chassis – the mud surface of Hakskeen Pan has a high salt content, and once the Car starts running, the salt-laden dust will get everywhere and start corroding the metal surfaces. To prevent this corrosion, we’re treating all of the vulnerable metal bits. The titanium panels will be OK as they are – titanium is the tough guy in the rear chassis. The aluminium will need to be anodised. This is an electrolytic process which involves immersing the aluminium chassis components in a conductive ‘electrolyte’ solution (in this case, chromic acid). An electrical current is then passed through the solution, with the aluminium component as the positive contact, or anode – hence ‘anodising’. The end result is a very thick oxide layer on the aluminium, which will protect the metal against salt corrosion.
This anodising process only works for aluminium, so all the steel bits will need painting in some way. We’re going to use a treatment called kephos (pronounced kee-foss). Kephos is a very tough, very thin coating (about 10-15 microns – less than a fifth of the thickness of a human hair) which will protect the metal and at the same time allow us to see if there are any cracks in the metal underneath. This will be finished in the next few weeks, after which we will join all the bits together for the first time – and if you will forgive the Americanism, it’s going to look awesome!